Gurasu Crystal Manufacturing Process
- Posted on
- By Joanna Maya
- Posted in crystal manufacturing process
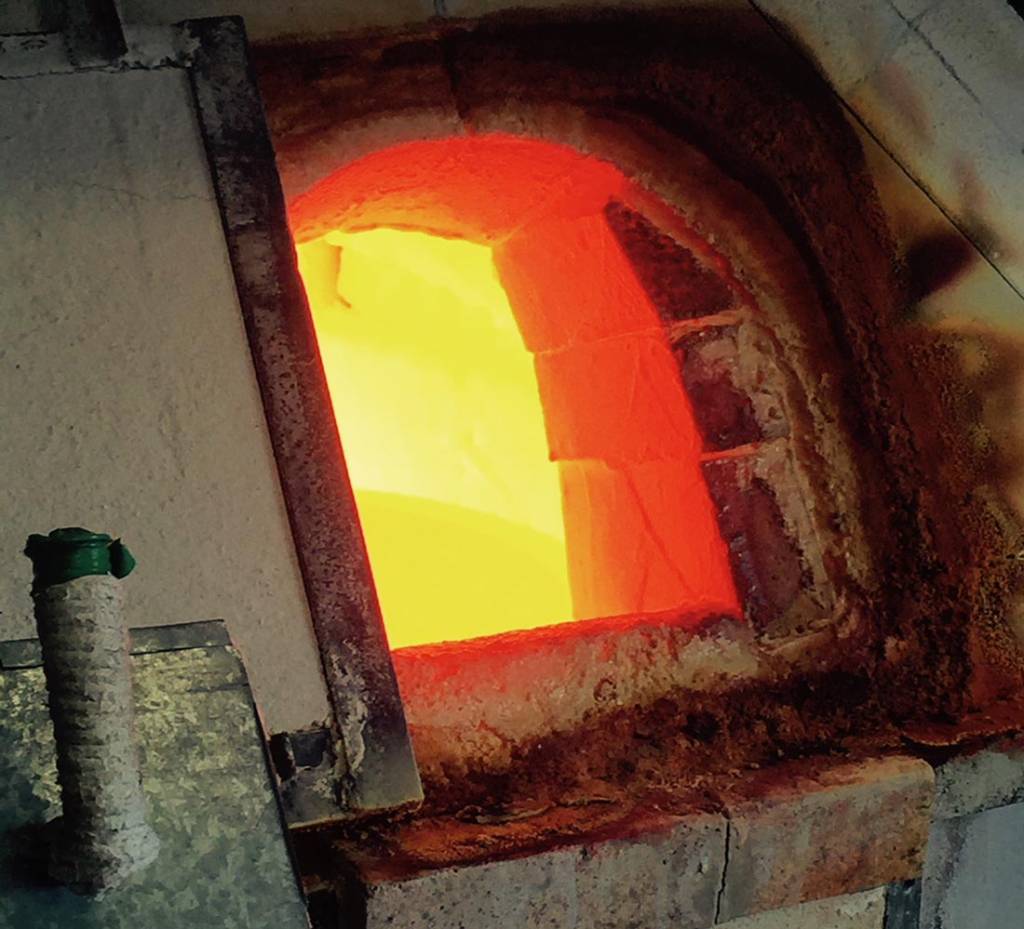
Would you like to know how our crystal is made? I very much belive that if we support traditional technics of crafstmanship and heritage industries they will continue operating and making high quality, handmade items for years to come. Although, handmade products are nowadays more expensive, due to a number of factors i.e. diminishing number of skilled craftsmen and young generation unwilling to be taking up the courses in heritage industries, the handmade products will become even more precious items to look after and enjoy.
In this article, I would like to focus on the first two stages of crystal making processes, namely the batch house and the hot-end.
Introduction
Modern crystal factories are three-part operations: the batch house, the hot end , and the cold end. The batch house handles the raw materials; the hot end handles the furnaces, forming machines, and annealing ovens; the cold end handles the cutting, decorating, product inspection and packaging.
BATCH HOUSE
A batch of the crystal is made of a special mixture of silicic sand, calcined soda, minium, potash and calcite or limestone. Also discolouring materials are added to those ingredients to remove undesired colours. The mixture is then put into melting tanks where it is melted at 1450˚C (2640˚F).
HOT END
Glassblowing is historically the most used technique for creating crystal products and still the most valued technique nowadays, because of the craftsman’s intimacy with the material, and almost infinite opportunity for creativity and variation at almost every stage of the process. “Blown crystal” refers only to individually hand-made items but can include the use of molds for shaping, ribbing, and spiking to produce decorative items or certain shapes of glassware.
The tip of the blowpipe is first preheated; then dipped on the molten glass in the furnace. The molten glass is gathered on to the blowpipe in much the same way that honey is picked up on a dipper.
Free-blowing
This method held a pre-eminent position in glass forming ever since its introduction in the middle of the 1stcentury BC until the late 19thcentury and is still widely used nowadays as a glass forming technique.
The process of free-blowing involves the blowing of short puffs of air into a molten portion of glass called a gather which has been spooled at one end of the blowpipe. The glassworker can then quickly inflate the molten glass to a coherent blob and work it into the desired shape. Skilled workers are capable of shaping almost any vessel forms by rotating the pipe, swinging it and controlling the temperature of the piece while they blow. One of the example of a free-blown item we sell is SOAP pendant lamp by Bomma. SOAP lamp has evolved from working with organic, freely blown glass and experimenting with coating technologies. This is the reason why each lamp comes in a slightly different shape and size.
Mold-blowing
A glob of molten glass is placed on the end of the blowpipe which is then inflated into a wooden or metal carved mold.
In this way, the shape and the texture of the glass sphere are determined by the design on the interior of the mold.
Once the vessel is formed, one can add a stem, pulling a small glob of glass away off the sphere and finishing it with a round foot. This is also a time to add any handles or other shapes according to the vessel design. Several people working synchronically is needed to make a crystal product.
Almost all crystalware made nowadays are made in either wooden or graphite molds. It would be impossible to achieve a desired shape and size of a glass whether it be in a single or higher number without the mold.
Molded crystal, which is also known as the pressed crystal can be made by machine or by hand. It is a form of glass made using a plunger to press molten glass into a mold.
Annealing
When the temperature of the product is 500˚C and the product is properly formed (be it blown or pressed, it is ready for cooling. As crystal product cools, it shrinks and solidifies. The cooling itself must be slow so as to prevent tension, which may cause cracking during further processing phases. Even cooling is achieved by annealing. An annealing oven heats the product to about 580˚C then cools it, depending on the crystal thickness, from 20 minutes to as long as up to several days. The thicker the crystal, the longer the annealing process.
In the next post, we will explain the final stage of crystal making called the cold end.
I hope you enjoyed reading this post and found it informative and easy to understand.